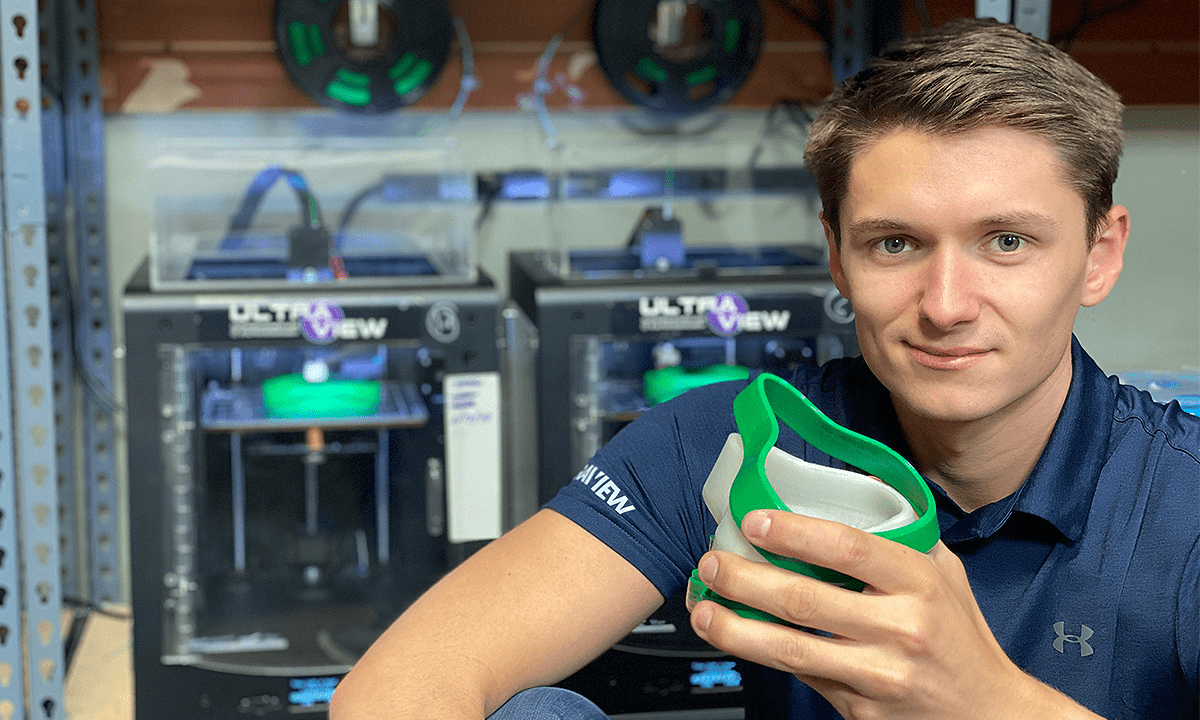
Apr 07, 2020 - Atlanta, GA
Engineers Kolby Hanley and Lee Whitcher leverage just-in-time manufacturing to create respirator parts to address the shortage of health care equipment
ATLANTA – April 7, 2020 –Personal Protective Equipment (PPE) and other medical supplies to manage COVID-19 complications are in short supply locally as well as globally. Many engineers from Georgia Tech and beyond are doing their part in the fight against COVID, and Kolby Hanley is one of them. A recent Materials Science Engineering graduate, Hanley has turned his company’s warehouse, using all of his 3D printers, into a rapid response center to create respirator parts.
Hanley has partnered with Lee Whitcher, a fellow Georgia Tech aerospace engineer, who spearheads the group AtlantaBeatsCOVID.com. The consortium is comprised of makers from the Atlanta community who feel they have something to contribute to the fight against COVID.
“I put out a call to everyone I knew, and within 24 hours I had 60 people from maker spaces all over the Atlanta area,” said Whitcher. “Kolby expressed an interest in helping with his vast array of 3D printers that his company UltraView traditionally uses to make archery parts.”
Hanley’s facility specializes in rapid prototyping, which made it a perfect place to 3D print molds based on Whitcher’s designs. These molds are then used to create the respirator parts that fit over a patient’s nose and mouth to facilitate breathing.
“I’ve been working directly with Lee every day,” said Hanley. “We go back and forth of the design of the mold, and he’s getting really close to perfecting it. After that’s done, we will create casting kits that we can send to people throughout the state, so anyone can use the molds to make respirator masks.”
The Making of a Kit
Hanley’s expertise in design for manufacturing is driving the creation of the molds and kits. The molding kit is a two-part piece, 3D printed using ABS (Acrylonitrile Butadiene Styrene) plastic that is acetone vapor smoothed to a mirror finish (green pieces in image below). Silicon can then be poured into the mold to create the much-needed respirator parts (the white piece in image below). The parts will then be shipped to a central location in Georgia, yet to be determined, and then sent out to healthcare facilities where they are needed most.
“You have to get the mold kit 100 percent correct before others can start using them,” said Hanley, who’s goal is to have the kits created and then open source the design so anyone in the world can print the kits. “That’s why it’s all Lee and I have been working on for the last two weeks.”
The ABS plastic is also a critical part of the mold making. It is an extremely smooth 3D printed material that is imperative to keeping the virus out.
“The 3D printing can only get you so far,” said Whitcher. “The ABS material that Kolby uses for the respirator part is what keeps the virus out, as it has to seal around the patients face.”
Hanley did run into a barrier to get the ABS material for creating the respirator part. It’s a common material, but he doesn’t carry it at his facility. And Amazon wasn’t going to be able to deliver it until late April. Hanley had to drive across the state to find a store that was open and selling the material.
AtlantaBeatsCOVID.com Partnership
As the founder of AtlantaBeatsCOVID.com, Whitcher continually works on the design of the kit and respirator mask, while Hanley works to implement his designs until they get it right.
“Basically, Lee tells me what to do and I do it,” said Hanley. “I then drop the latest prototype to Lee every morning. My company is basically a rapid prototyping hub for Lee.”
As Whitcher says, “Kolby is my personal printer, and amazing to work with.”
The ultimate goal is for everything to be open sourced with directions on how to use the kits to make the respirator masks. Whitcher has similar plans for intubation enclosure he’s been working on as well. While this project isn’t one that Hanley works on, it’s critical to the COVID response.
“Following the lead of a doctor in the Philippines, we are working on a prototype of a shroud that covers a patient’s chest and head as the intubation tube is pulled out,” said Whitcher. “Normally when an intubation tube comes out, fluids disperse everywhere. That’s what we are trying to mitigate to contain the spread of the virus.”
The shroud is a sanitized enclosure with features that allow healthcare workers to run vent tubes to the patient. Whitcher has been simulating the procedure and hopes to have a prototype ready soon.
The Motivation
For Hanley, he realized that with his 3D printers, he had the ability to do just-in-time manufacturing for the fight against COVID.
“Everyone is out to flatten the curve, and everything needs to happen very fast,” said Hanley. “I realized the design and manufacturing that go into these final use parts to make the kits is exactly what we do at UltraView. So, it was clear I should help with this.”
Hanley goes on to explain the turn around time for responding to the virus.
“Normally for manufacturing efforts, it’s a two-week lead time, and that’s fast by industry standards,” said Hanley. “With just-in-time manufacturing you have two days to get ahead of it. The faster we can manufacture and make kits into an open source design, it will help others create the parts in an exponential and impactful way.”
For Whitcher and his creation of AtlantaBeatsCOVID.com, he felt he had the particular skill set to help with the situation. His connection to the maker community of Atlanta was something he could leverage for the cause.
“I felt morally compelled to do this,” said Whitcher. “On the first day of lockdown, I considered using the time to finish my PhD thesis, but I decided that was selfish – my thesis could be finished at any time. But now is the only time I have to contribute to this fight.”
For now, Hanley and Whitcher continue to perfect the molding kit design so it can be open sourced as soon as possible. As for AtlantaBeatsCOVID.com’s other designs, those are a continual works in progress as well at press time.